Effective Repair Strategies for Hydraulic Pump Failures in Injection Moulding Machines
Hydraulic pump failures in machine injection moulding can lead to costly downtime and production delays. Understanding effective repair strategies can help you minimize disruptions and maintain smooth operations.
Repair Strategies for Common Failures:
- Seal Replacement for Leakage: Leaks often result from worn-out seals. Regularly inspect seals for signs of wear and replace them promptly to prevent oil leakage and maintain optimal pressure in the system.
- Filter Replacement for Overheating and Cavitation: Clogged or dirty filters can lead to overheating and cavitation. Implement a routine filter inspection and replacement schedule to ensure clean hydraulic fluid and reduce the risk of pump failure.
- Oil Quality Checks: The quality of hydraulic oil is crucial for pump performance. Regularly test oil quality and replace it if contaminants are present. This helps prevent overheating and internal component damage.
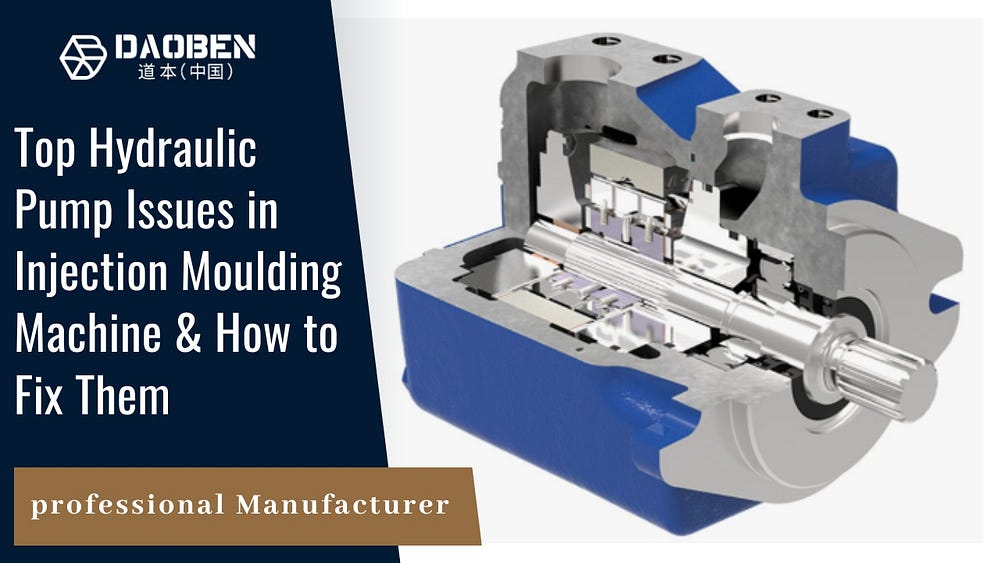
Proactive Maintenance Tips:
- Implement a regular maintenance schedule to check fluid levels, filters, and seals.
- Train operators to recognize early signs of hydraulic pump issues.
- Keep a stock of essential replacement parts to minimize repair time.
By adopting these repair strategies and proactive maintenance practices, you can reduce the likelihood of hydraulic pump failures and maintain efficient injection moulding operations.
Comments
Post a Comment