Hydraulic Plastic Moulding Machine: Revolutionize Production!
A hydraulic plastic molding machine uses hydraulic systems to produce plastic parts. It efficiently shapes thermoplastic or thermosetting polymers into various forms.
First Impression
Hydraulic plastic molding machines are pivotal in manufacturing processes, offering precise production of plastic components. These machines work under the principle of using pressurized hydraulic fluids to clamp the mold and inject molten plastic into it, where it cools and hardens into the final shape.
Their robust design and high clamping force make them suitable for large-scale production with consistent quality. With advancements in control technologies, these machines now offer improved energy efficiency, faster cycle times, and enhanced precision. Industries from automotive to consumer goods rely on this technology for their plastic parts fabrication, making it a cornerstone of modern manufacturing. Ensuring seamless operation, these machines also integrate with automated systems for streamlined production lines.
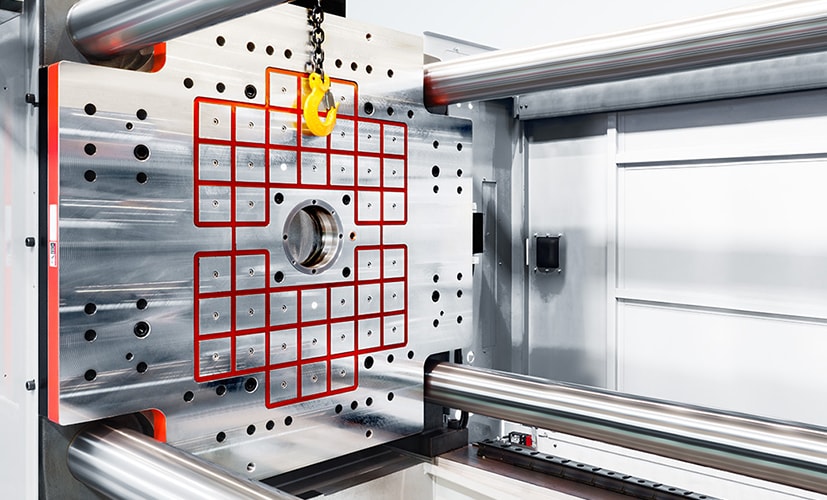
The Mechanics Of Hydraulic Plastic Moulding Machines
Understanding the mechanics of hydraulic molding machines is like peeking under the hood of a car. To shape plastic into countless products, these powerful machines use precision and force. Let's explore the inner workings that make this transformation possible.
Core Components And Their Functions
Hydraulic plastic moulding machines consist of several key components, each critical to the moulding process. The machine's success depends on these parts working in harmony.
- Injection Unit: Heats and injects the plastic into the mould.
- Hydraulic System: Powers the machine with fluid pressure.
- Clamping Unit: Holds and clamps the mould in place during the process.
- Mould: The cavity that shapes the plastic into the final product.
- Control System: Manages the operation timings and settings.
How Hydraulics Empower Moulding
The power of hydraulics lies in the controlled pressure it can apply. Here's a quick overview of how they empower plastic moulding:
- Hydraulic pumps generate pressure that moves cylinders.
- This movement controls the clamping and injection processes.
- Consistent force ensures uniformity in product quality.
- Variable pressure allows for intricate designs in moulding.
Comparing Hydraulic To Electric Moulding Machines
In the world of plastic manufacturing, hydraulic molding machine and electric moulding machines stand out as titans. Each has unique traits shaping production outcomes. Let's dissect these machine types, looking at energy efficiency, precision, and durability.
Energy Efficiency Face-off
Energy consumption is a critical factor in choosing the right machine. Electric machines shine here, often reducing energy use by up to 50% compared to hydraulic counterparts.
- Electric Machines: Employ efficient servo motors, conserving energy.
- Hydraulic Machines: Require constant power to maintain pressure.
Precision And Control
Precision molds quality products. Electric machines excel with superior control and repeatability.
Machine Type | Precision Level | Control Consistency |
---|---|---|
Electric | High | Very Consistent |
Hydraulic | Variable | Less Consistent |
Maintenance And Durability
Machine longevity is non-negotiable. Hydraulic machines are robust, enduring rigorous settings. Electric models need less maintenance but may have higher repair costs.
Points to consider:
- Hydraulic: More tolerant to harsh environments.
- Electric: Require specialized servicing.
Applications In Various Industries
Exploring the versatility of Hydraulic Plastic Moulding Machines unveils their critical role across various industries. These powerful machines shape countless products we use every day. hydraulic molding machine is integral in manufacturing from the smallest components to larger structural parts. Let's dive into specific applications within different sectors:
Automotive Industry Advances
- Innovative car parts production
- Durable plastic components for vehicles
- Enhanced precision in manufacturing
The automotive sector relies heavily on hydraulic moulding to create parts that are both durable and lightweight. This technology has led to advancements in the production of items such as dashboards, bumpers, and internal mechanisms. Precision and strength are paramount here, as these components play a vital role in vehicle safety and performance.
Consumer Goods And Packaging
Consumer Product | Packaging Solutions |
---|---|
Toys and household items | Food containers and bottles |
Electronic housings | Tough packaging materials |
The vast universe of consumer goods is home to myriad products moulded from plastic. The role of hydraulic moulding machines in creating packaging solutions cannot be understated. They produce a variety of items, from protective packaging that ensures product safety during shipping to the actual containers housing consumer products.
Medical Equipment And Safety
- Critical medical devices and housings
- Sanitary product manufacturing
- High standards for safety and cleanliness
Saving lives and maintaining health also come under the purview of hydraulic plastic moulding. With its capability to fashion medical-grade plastic parts, this process is essential in producing equipment like surgical tools, diagnostic devices, and hospital supplies. The medical industry favors this method for its ability to meet the high standards of safety, hygiene, and precision required in healthcare environments.
Technological Advancements In Hydraulic Moulding
In the world of manufacturing, hydraulic plastic moulding machines stand out for their ability to produce high-quality plastic parts with remarkable precision. Ongoing technology improvements help these machines work smarter, faster, and more sustainably.
Innovations In Machine Intelligence
Today's hydraulic moulding machines come equipped with advanced sensors and control systems. These technologies enable the machines to monitor their own operations in real-time. Essential functions, such as pressure adjustments and timing, are finely tuned by intelligent software. This results in:
- Better product quality due to precise control.
- Reduced waste as errors are minimized.
- Improved efficiency through self-optimization.
Sustainability Measures
The drive towards sustainability is fundamental in modern manufacturing. Hydraulic moulding machines now boast features like:
- Energy recovery systems that reduce power consumption.
- Biodegradable hydraulic fluids that are eco-friendly.
- Advanced clamping systems that lower energy use.
Such enhancements make plastic production greener and more cost-effective.
Customization And Modular Design
Custom solutions are vital for different production needs. Modern hydraulic moulding machines feature:
- Modular components for easy upgrades and customization.
- Flexible software that adapts to various moulding processes.
- Interchangeable parts, allowing swift response to change.
These adaptations mean businesses can tailor machines to specific tasks, optimizing production and staying current with industry demands.
Navigating The Purchase Of Hydraulic Moulding Machines
Choosing the right hydraulic plastic moulding machine can transform your production line. These powerful devices shape countless products we use daily. Before you invest, understand your requirements, evaluate costs and benefits, and consider vendors and their support. Let's explore how to make an informed decision.
Assessing Your Production Needs
Identify the scale and specifics of your operation. Assess aspects such as:
- Moulding capacity — the volume of products needed.
- Material type — the plastics you'll be working with.
- Complexity of designs — simple shapes or intricate details?
- Space constraints — the size available in your facility.
Cost-benefit Analysis
Understanding the return on investment is key. Weigh initial costs against long-term benefits. Consider:
Cost Factor | Benefit |
---|---|
Price of machine | Product quality improvement |
Installation expenses | Increased production speed |
Maintenance outlay | Reduced labor costs |
Training for operators | Less material waste |
Vendor Selection And After-sales Service
Select a vendor not just on the injection molding machine price, but reliability and service quality. Ensure:
- They have good reviews and industry credibility.
- Support is accessible, with a responsive after-sales team.
- Availability of spare parts is guaranteed for the machine's life.
- Training is available for your team to operate the machine efficiently.

Future Trends And Market Outlook
The hydraulic molding machine industry stands on the cusp of transformative changes. Technological advancements and global shifts towards sustainability are steering the future of plastic moulding. The market outlook is vibrant with anticipated growth, driven by innovation and evolving demands. Let's delve into the groundbreaking trends that will shape this sector.
Integration With Industry 4.0
The marriage of hydraulic plastic moulding machines with Industry 4.0 is creating smart factories. Future machines will boast self-optimizing capabilities. Enhanced connectivity will enable real-time monitoring and analytics. This integration promises improved efficiency, higher product quality, and decreased downtime.
- Seamless connectivity between devices
- Remote monitoring and diagnostics
- Data analytics for predictive maintenance
Shift Towards Bio-plastics
Environmental consciousness is nudging the industry towards bio-plastics. These sustainable materials are rising in popularity as eco-friendly alternatives to traditional polymers. Hydraulic molding machine are adapting to handle these new materials, leveraging their renewable and biodegradable advantages to meet market demands.
Material | Benefits | Usage |
---|---|---|
PLA | Biodegradable | Packaging |
PET | Recyclable | Bottles |
PHA | Biodegradable | Medical |
Evolving Regulatory Compliance
Regulations are transforming to reflect the new priorities of safety and sustainability. Hydraulic plastic moulding machines need to comply with stricter standards. Manufacturers are focusing on machines that produce less waste and consume less energy. Compliance will be critical for market access and consumer trust.
- Energy-efficient operations to reduce carbon footprint
- Reduced waste production in the moulding process
- Use of non-toxic lubricants and fluids
Frequently Asked Questions Of Hydraulic Molding Machine
What Is A Hydraulic Plastic Moulding Machine?
A hydraulic plastic moulding machine is a manufacturing device. It uses hydraulic force to mold plastic into desired shapes. The process is well-suited for high-volume production of plastic parts.
How Does Hydraulic Plastic Moulding Work?
Hydraulic plastic moulding works by applying pressurized hydraulic fluid. This fluid actuates the machine's clamping and injection mechanisms. This precision allows intricate plastic parts to be crafted efficiently.
What Are The Advantages Of Hydraulic Moulding Machines?
Hydraulic moulding machines offer robust clamping force and precision. They are reliable for producing large volumes of parts. Their designs often result in a consistent and high-quality output.
Can Hydraulic Machines Mold Complex Parts?
Yes, hydraulic machines are capable of molding complex parts. Their precise control over the molding process allows for intricate designs and details in the final product.
Final Thought
Understanding hydraulic plastic molding machines is key to optimizing production. These robust systems offer precision, efficiency, and reliability for manufacturers. As technology advances, they continue to evolve. Embrace the versatility of hydraulic machines to stay ahead in the competitive plastics market.
Don't forget to maintain and update your equipment for peak performance.
Comments
Post a Comment